Componentes del hormigón: características, proporciones,
Los componentes del concreto determinan su calidad, resistencia, marca y afiliación de clase, así como una serie de otros parámetros y características del mortero y el material endurecido. Le diremos qué proporción de componentes de concreto se considera normal y también le mostraremos cómo calcular los componentes para concreto.

La composición de la mezcla de hormigón.
Información general

El concreto se llama piedra artificial, que se produce mezclando el aglutinante con agua con la introducción de agregados grandes y pequeños, así como con varios aditivos específicos: plastificantes, repelentes del agua, antisépticos, etc. También hay hormigones anhidros, como el asfalto y algunos otros.
Hablaremos de los hormigones tradicionales utilizados en la ingeniería civil: las mezclas a base de cemento como aglutinante, ya que además del cemento, se utilizan varias escorias, polímeros, resinas, etc.

Por lo tanto, para la producción de hormigón de cemento usar tales ingredientes:
- Cemento portland (a veces cemento de escoria de endurecimiento rápido): polvo mineral, que reacciona a la hidratación con agua y se endurece con la formación de una piedra densa y sólida. Juega el papel de pegamento, que une todos los componentes en una estructura monolítica;
- Arena - agregado fino, que contribuye al ahorro de cemento y desempeña un papel en la creación de un marco de estructura fina que evita la deformación y la formación de microfisuras durante los procesos de endurecimiento y contracción
- Escombros - agregado grande, que, junto con la arena, reduce el costo de la mezcla, ya que el precio de los agregados es bajo. Previene la fractura durante la contracción y el endurecimiento, crea un marco estructural y aumenta el módulo elástico del material, y también reduce su fluencia
- El agua - uno de los componentes más importantes de la mezcla, que está involucrado en el proceso de hidratación del cemento y la formación de pegamento endurecedor, y es también el medio donde se produce la mezcla, la interacción y la distribución uniforme de los componentes restantes de la solución;
- Aditivos - Plastificantes, repelentes al agua, antisépticos, sellos y otros. Aumentar ciertos indicadores, como la fluidez, resistencia a la humedad, resistencia a las heladas, inercia química y biológica, densidad, etc.

Presta atencion Como puede ver, la composición de la mezcla de hormigón es heterogénea, por lo que la calidad del producto depende de muchas variables. Los grados de concreto y la proporción de componentes, así como su calidad y tipo están directamente relacionados.
Requisitos del componente

Ahora vamos a hablar de los componentes con más detalle. Uno de los componentes principales, sin los cuales no pasa nada, es el cemento. En la construcción, como regla general, se utiliza el cemento Portland de los grados M300 - M500, sin embargo, se debe tener en cuenta que para la producción de concreto del grado M350 se requiere un cemento de al menos M500, y el cemento M400 producirá concreto del grado no superior a M250.
La marca muestra la resistencia a la compresión del material, y para la construcción individual y civil, la resistencia del M250 - M350 es suficiente, por lo que puede usar el producto de la marca M500 de forma segura incluso para nodos críticos. El único comentario es que la proporción de componentes en concreto para la cimentación debe seleccionarse con mayor cuidado, por lo tanto, el mortero de calidad comercial de la fábrica generalmente se usa para concreto en esta parte de la casa.

La piedra triturada es otro ingrediente importante de la mezcla. Se cree que la resistencia de los escombros debe ser aproximadamente el doble de la resistencia de diseño del concreto, que se obtiene dentro de los 28 días. Esto se debe al hecho de que la piedra de hormigón madura durante varios años y gana resistencia adicional, que como resultado se vuelve aproximadamente igual a la resistencia de los escombros, que permanece igual para este indicador.
Para la fabricación de concreto tradicional es suficiente resistencia escombros de grava, que es de aproximadamente 800 - 1000 kg / sq. cm, que es suficiente para una marca de material de hormigón M450. Para la producción de productos de la marca M100 - M300, puede usar escombros de piedra caliza, pero el más duradero y costoso es la piedra de granito, que se utiliza con mayor frecuencia para la producción de variedades de concreto especiales, de carretera y de alta resistencia.
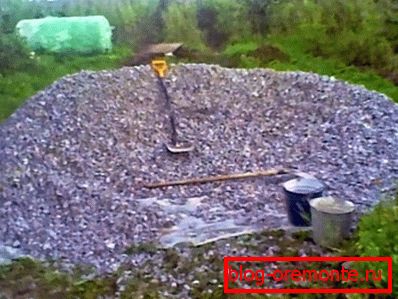
Presta atencion A veces, la piedra triturada de piedra caliza utilizada deliberadamente se usa intencionalmente, por ejemplo, cuando se espera la molienda o corte de concreto reforzado con círculos de diamante. También de esta manera, se facilita la perforación diamantina de agujeros en concreto.
La arena se puede usar en la carrera o en el río, lavada de arcilla e impurezas similares al polvo. La fracción media y pequeña más utilizada es la más utilizada, y para la fabricación de arena arenosa, se necesita arena de granulometría.
Si hablamos de aditivos, vale la pena señalar inmediatamente que la introducción de productos químicos de alta calidad solo es posible en las condiciones de producción de la fábrica. Los componentes para la producción de concreto aireado, por ejemplo, incluyen polvo de aluminio, pastas y emulsiones, cuya dosificación debe ser precisa.

Del mismo modo, los componentes para la producción de concreto de espuma - espumantes - también deben coincidir exactamente con la receta, ya que los componentes para concreto de espuma pueden dañar el material y reducir su marca con una ligera desviación de la norma.
Calculo

Como se mencionó, la proporción de componentes es el parámetro más importante en la producción de mezcla de concreto. La instrucción clásica asume dicha proporción (cemento / piedra triturada / arena / agua): 1: 4: 2: 0.5. Números en proporción a las fracciones en masa.
Por supuesto, esta proporción es bastante arbitraria y aproximadamente, ya que en la práctica estamos tratando con materiales reales que tienen muchas impurezas, absorben el agua de manera diferente y tienen una humedad inicial diferente. Para una definición más precisa de la receta, debe usar tablas y programas informáticos especiales, sin embargo, tampoco garantizan que el producto obtenido corresponda a la marca o clase esperada.
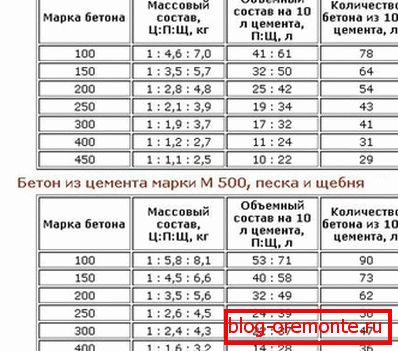
Incluso en las condiciones de las fábricas donde hay laboratorios y equipos especiales para pesar, dosificar, mezclar y preparar componentes, es necesario realizar pruebas obligatorias de la resistencia de la piedra obtenida, y solo después de eso podemos hablar con confianza de la clase o afiliación de la marca del material obtenido.
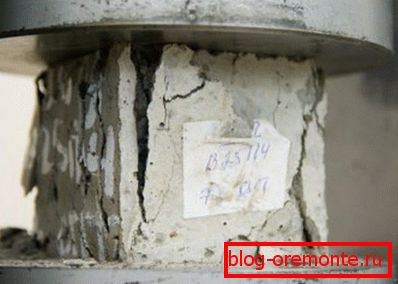
Existe un método para calcular la composición en condiciones de campo:
- Vierta los escombros en el cubo de diez litros hasta la parte superior y agite el recipiente para que la piedra se distribuya uniformemente sobre el volumen del cubo;
- Usando una jarra de un litro u otros utensilios de medición, agregamos agua al cubo con grava hasta que alcance el mismo nivel. Recuerda la cantidad de agua. Así que determinamos el volumen requerido de arena;
- Ahora vierta los escombros y llene el cubo con arena seca hasta el punto que acabamos de identificar. Luego, agregue nuevamente el agua con un recipiente medidor (preferiblemente el mismo) hasta que la arena se cubra con agua. La cantidad de agua será igual al volumen requerido de cemento;
- Para determinar la cantidad óptima de agua, debe tomar 50 - 60% del volumen de cemento, que encontramos experimentalmente en el párrafo anterior;
- Al final, debe tomar el volumen calculado de hormigonado y dividirlo por el volumen de una cubeta - 10 litros, y multiplicar el número resultante por los valores calculados previamente para cada componente.

Presta atencion Para trabajos exigentes, use concreto premezclado de fabricantes probados, ya que es problemático hacer un producto de calidad en el campo por varias razones convincentes.
Conclusión
Качество, тип и соотношение компонентов определяют марку бетонного раствора и прочность будущего изделия. Для определения оптимальных пропорций существуют различные способы, однако добиться в полевых условиях точного соответствия проблематично (см.также статью «Бетон М150 – технические характеристики и особенности применения»).
El video en este artículo te ayudará a ver esto.